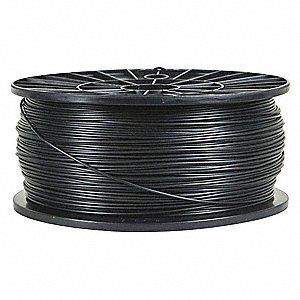
Medical FEP Tubing: Workplace Safety Tips to Consider
Fluoropolymers such as perfluoroalkoxy alkane (PFA), polyvinylidene fluoride (PVDF), polytetrafluoroethylene (PTFE), and fluorinated ethylene propylene (FEP) are known for their use in many industries. These materials - specifically FEP - have outstanding properties,...
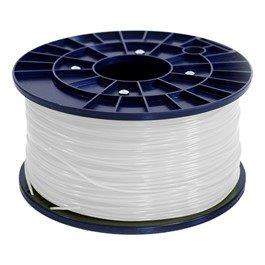
A Closer Look at Tubing Pressure Specifications
Tubing systems are complicated mechanisms. Each industry and application requires certain types of piping set in a specific environment. You need to align several factors, so the processed substance efficiently flows through the network of hoses to its intended...
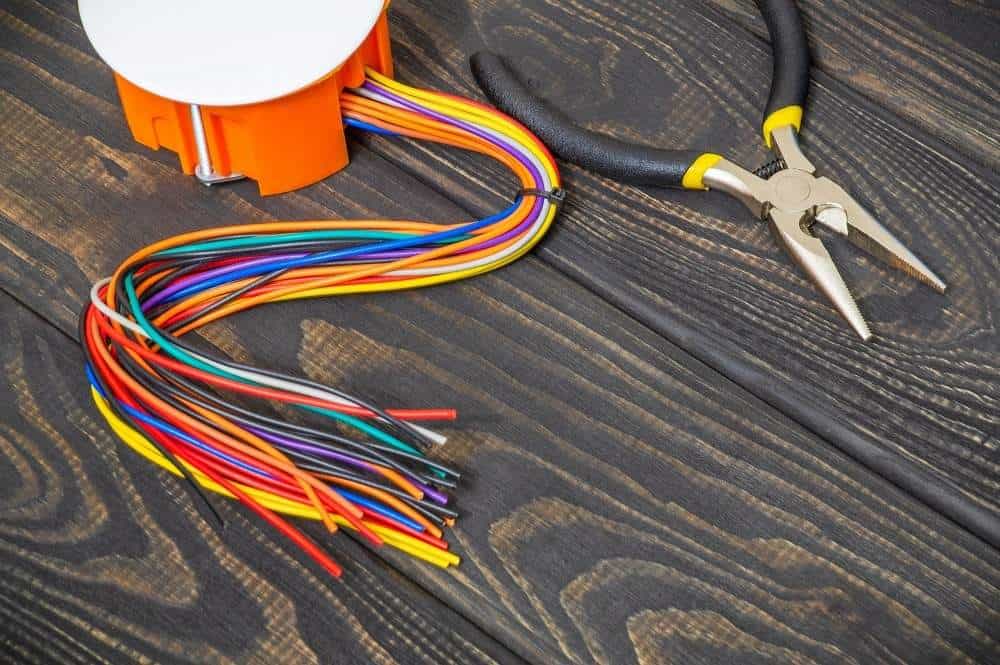
Upsides of PTFE Cable and its Applications
One of the most amazing materials invented in the last century is the plastic called polytetrafluoroethylene or PTFE. This fluoropolymer is made of carbon and fluorine atoms, which have a unique molecular arrangement. Its distinct composition is the reason for its...
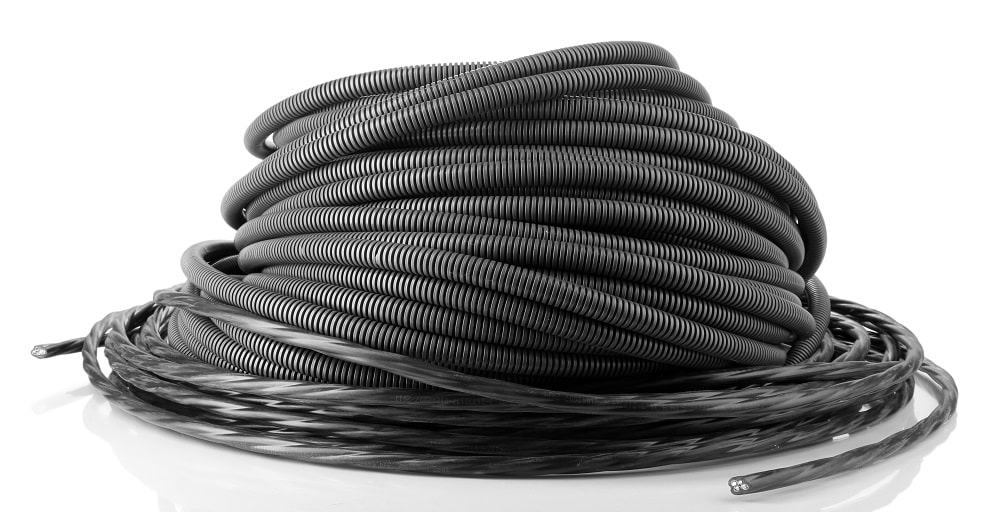
Convoluted Tubing: What You Need to Know
Tubes are long, hollow, cylindrical objects made of glass, metal, or plastic. They're designed for handling liquids or gases. They can also be used as a protective casing for wires and cables. One, in particular, is called convoluted tubing. Its name comes from its...
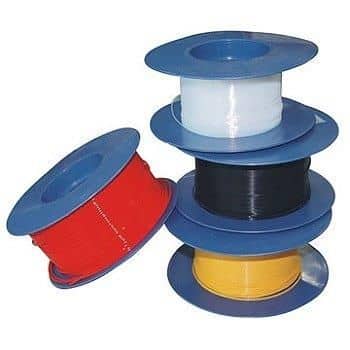
Everything You Need to Know About Heat Shrink Tubing
Back in the 1900s, the discovery of synthetic plastics opened up ways to create materials that were unlike anything people have ever heard of before. One of them was heat shrink tubing, which was eventually invented by Raychem Corporation in the 1950s. It was a thin...