Heat Shrink Tubing Recovery Process
Extreme caution must be exercised in heating the PTFE during the shrinking process. The PTFE Tubing must be heated evenly to the gel state to insure complete recovery. PTFE shrink tube will become completely clear when it reaches it gel state at about 624°F. After the material has reached its gel state do not continue to heat, the material is now ready to begin the cooling and shrinking phase. PTFE will start to recover once the cooling process has begun and the material comes out of its gel state. Once the material has completely cooled the PTFE’s appearance will be its normal milky white color.
PTFE Heat Shrink Tubing will tend to split longitudinally if tubing is not allowed to recover to about 75 % of its expanded diameter or if it is over heated during shrinking.
How To Shrink PTFE Heat Shrink Tubing
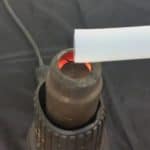
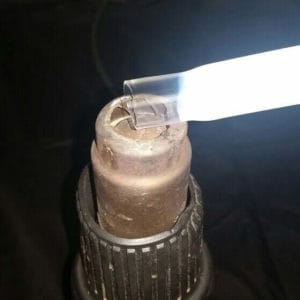
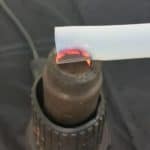
ALWAYS assure good ventilation in your work area before starting the heat shrink process. Shrinking with direct flames or burning of Fluoropolymers may cause dizziness and flu like symptoms.
Resins | FEP Tubing | FEP Roll Cover | PTFE Tubing | Dual Wall PTFE / FEP |
---|---|---|---|---|
Working Temp. | 400° F | 400° F | 500° F | 450° F |
Shrink Temp. | 230° F | 350° F | 624° F | 624° F |
Heat Guns | Preferred | Preferred | Not Preferred | Not Preferred |
Ovens | Preferred | Not Preferred | Preferred | Preferred |
Shrinking Process
The Properties of Heat Shrinkable PTFE
At Tef Cap Industries, our heat-shrinkable PTFE solutions are ideal for those seeking moisture-proof, tight bonds over terminals, splices, cables, connectors, and traditional wire setups. Some of the main properties of heat-shrinkable PTFE include the following:
- Single Wall Operating Temperature: Tef Cap’s PTFE material has a high operating temperature of up to 500 ° Fahrenheit, or 260° C. Our PTFE tubing solution materials can also handle temperatures as low as -328° F, or -200° C.Â
- Dual Wall Operating Temperature: Tef Cap’s Dual Wall material (PTFE/FEP) has a high operating temperature of up to 450 ° Fahrenheit, or 232° C. Our PTFE and FEP tubing solution materials can also handle temperatures as low as -328° F, or -200° C.
- Protection Abilities: Provides tight, moisture-resistant bonds and protection. Heat-shrinkable tubing protects against corrosion, shock, moisture, and extreme environmental conditions (including high or excessive heat).
- Availability: Tef Cap Industries provides heat-shrinkable PTFE solutions in various dimensions, sizes, and shrink ratios for all fluoropolymer heat-shrinkable tubing needs. Light and Standard solutions are available in multiple models to suit your project’s specifications. Our heat-shrinkable polyolefin tubing is ideal for those looking to shrink materials, whether you are currently using Teflon PTFE or FEP tubing materials.
Industries that Frequently Make Use of Heat Shrinkable PTFE
Whether you’re interested in Teflon FEP shrink covers or shrinkable PTFE for a new system you’re investing in, Tef Cap Industries has a solution for you. Industries that frequently make use of heat-shrinkable PTFE include:
- Chemical/Industrial
- Healthcare
- Aerospace
- Pharmaceutical
- Semiconductor
- Food & Beverage
- Solar Panel Manufacturing
How Does Heat Shrinking Affect the Properties of PTFE Tubing?
- Size: When you choose to shrink PTFE tubing, it’s important to consider the original size of your tubing and the intended size you have in mind. Tef Cap Industries can work with you to determine if you require Light, Standard, or Dual-wall solutions.
- Conformity: We work to ensure seamless shrinking of Teflon PTFE tubing with any shrink ratios you desire.
- Tensile strength: Tef Cap Industries works to preserve and protect tensile strength during the heat-shrinking process. A controlled environment prevents overheating in the area without properly recovering the tubing.
- Flexibility: If tubing cannot recover to approximately 75% of its expanded diameter, the tube itself may split longitudinally. There is also a risk of overheating during shrinkage if not properly monitored or shrunk to a gel state at 624 F° in a controlled environment.
- Thickness: Exercising caution can ensure the thickness and strength of PTFE tubing when heating evenly.
- Surface finish: PTFE tubing, once shrunk at high temperatures, will turn to a clear, gel state.
It’s essential to ensure proper ventilation when beginning the heat-shrinking process. Direct or extreme open-flame high-temperature environments combined with Fluoropolymers can lead to flu-like symptoms and the onset of dizziness. Regarding encapsulation, heat shrinking, etching, thermoforming, or custom extrusions, look no further than Tel Cap Industries, the trusted go-to provider with over 80 years in business.
If you’re interested in bundling your existing tubing investments, sealing them, or protecting them, Tef Cap Industries is here to help. To learn more about our heat-shrinkable Teflon tubing and shrinking process or to request a quote, contact us online or call Tef Cap Industries at 610-692-2576.